In the field of modern decorative materials, bamboo charcoal wood veneer with water ripple texture has become increasingly popular due to its natural appearance, eco-friendliness, moisture resistance, and visual aesthetics. Particularly in high-end interiors such as hotels, commercial spaces, and luxury residences, this material offers both functionality and design appeal.
This article presents a comprehensive breakdown of the production steps of bamboo charcoal wood veneer with water ripple patterns, guiding B2B buyers and interior design professionals through the intricacies of its manufacturing process.
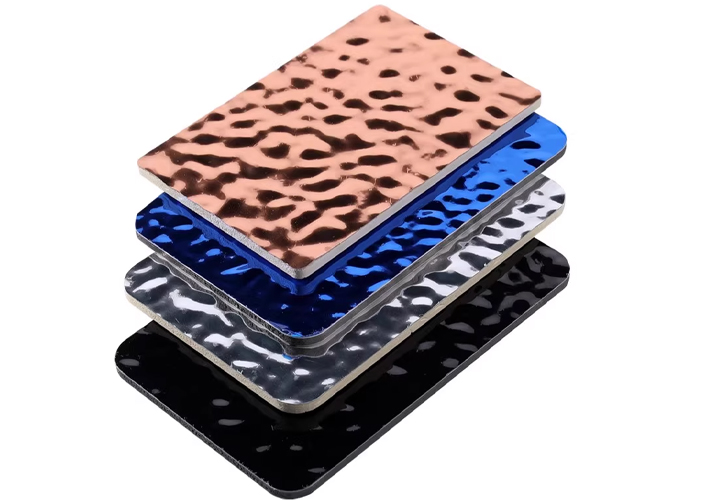
Table of Contents
ToggleIntroduction to Bamboo Charcoal Wood Veneer
Bamboo charcoal wood veneer is a decorative surface material that combines bamboo charcoal fiber with synthetic or natural resins to form a wood-like finish. It’s widely used for:
- Wall paneling
- Furniture cladding
- Ceiling applications
- Decorative partitions
The water ripple effect adds a flowing, three-dimensional look, making the material both decorative and dynamic in presentation.
Understanding the Water Ripple Texture
The water ripple design imitates gentle waves or water surfaces, offering an elegant visual rhythm. Technically, this texture is achieved by precision molds and embossing techniques during production.
Water ripple veneer is often found in:
- Hotel lobbies
- Reception areas
- Feature walls in commercial spaces
- Showrooms and art spaces
Raw Material Selection
a. Bamboo Sourcing
- Species: Moso bamboo (Phyllostachys edulis) is preferred due to its density, flexibility, and rapid renewability.
- Age of Harvest: Ideal between 4–6 years for best fiber maturity.
- Origin: Commonly sourced from provinces like Sichuan, Fujian, and Zhejiang in China.
b. Additives and Binders
- Eco-friendly resins like phenolic or melamine-based binders
- Non-toxic fire retardants and stabilizers
- UV stabilizers for outdoor-grade veneer
c. Surface Coating Materials
- Water-based PU or UV coatings
- Matte, semi-gloss, or high-gloss finishes depending on design intent
Pre-processing and Carbonization of Bamboo
a. Cutting and Splitting
Bamboo culms are cut, split, and trimmed into strips, then boiled to remove sugar and starch (which attract pests).
b. Drying
The strips are dried to a moisture content of 8–12%, critical for avoiding warping or cracking during pressing.
c. Carbonization Process
Carbonization enhances:
- Moisture resistance
- Insect and mold resistance
- Color stability (rich dark hue)
This is done in high-temperature kilns under controlled oxygen conditions. Final temperature can reach up to 700–800°C for high-grade charcoal effect.
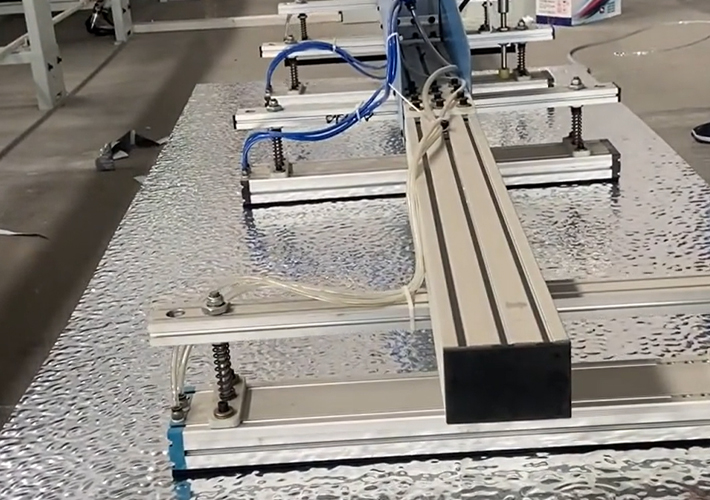
Fiber Extraction and Composite Base Preparation
a. Fiber Pulverization
The carbonized bamboo is ground into fine charcoal powder or fiber.
b. Mixing with Binders
Using industrial mixers, bamboo charcoal powder is combined with:
- Resins
- Colorants (if required)
- Stabilizers and fire retardants
The mixture forms the core base material for the veneer.
Substrate Forming and Drying
a. Panel Forming
The mixture is spread over a flat press mold or extruded into sheet form, often using:
- Hot press forming
- Roller extrusion technology
Panel thickness typically ranges from 3mm to 9mm, depending on application.
b. Drying/Curing
The formed sheets are oven-cured or UV cured depending on the resin type used. This ensures:
- Hardness
- Dimensional stability
- Adhesion quality
Pressing the Water Ripple Texture
This is a critical step for the visual appeal of the veneer.
a. Mold Design
Water ripple designs can vary in:
- Wave size (fine vs. bold)
- Direction (vertical, horizontal, random)
- Depth (shallow embossing vs. deep carving)
The mold is typically made of CNC-engraved steel or silicone-based materials.
b. Hot Pressing or Embossing
The pre-cured bamboo charcoal panels are sent through a texturing press machine:
- Temperature: 160–200°C
- Pressure: 20–30 MPa
- Duration: 30–60 seconds per panel
Multiple passes may be required for deep or multi-layer ripple effects.
Surface Coating and Finishing
a. Primer Application
- Fills pores and seals the surface
- Enhances coating adhesion
b. Base Coating
- Applied using roller coaters or spray systems
- Cured under UV lamps or hot air dryers
c. Final Top Coating
Available in:
- Glossy for luxury applications
- Matte for modern aesthetics
- Anti-fingerprint or anti-scratch for commercial use
d. Optional Treatments
- Brushing or sanding for natural texture feel
- Foil lamination or printing for special designs
Quality Inspection and Grading
a. Visual Inspection
- Color consistency
- Surface uniformity
- Texture clarity
b. Dimensional Checks
- Thickness tolerance (±0.2mm)
- Panel flatness
- Warp test
c. Performance Testing
- Fire resistance (ASTM E84 or EN 13501 standards)
- Formaldehyde emission (E0/E1 grade)
- Impact and abrasion resistance
Panels are sorted into A-grade (export quality) and B-grade (domestic or discounted use).
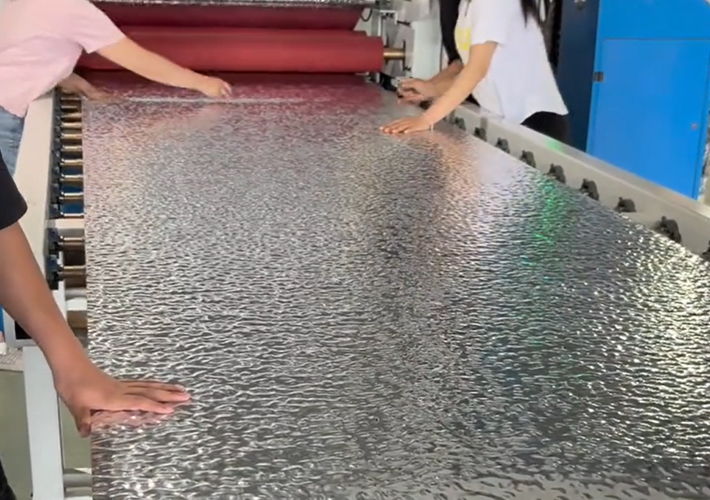
Packaging and Export Requirements
a. Standard Export Packaging
- PE protective film on panel surface
- Stacked on fumigated wooden pallets
- Wrapped with waterproof membranes
- Secured with steel belts and corner protectors
b. Labeling
- Batch number
- Panel size and thickness
- Production date
- QC inspection mark
c. Container Loading
- 20GP: ~7000–9000 m²
- 40HQ: ~15000–18000 m² depending on thickness
Customization Options for B2B Clients
B2B clients, especially interior contractors and distributors, often require:
a. Size Customization
- Standard sizes: 1220mm x 2440mm
- Optional: 600mm x 2800mm, or customized cutting
b. Pattern Customization
- Ripple amplitude and frequency
- Integration with grooved slats for acoustic performance
- Combination with metallic or stone finishes
c. Fire-Rated or Acoustic Variants
Panels can be produced to comply with Class A fire rating or have sound-absorbing backing materials for hotel and commercial projects.
Conclusion
The production of bamboo charcoal wood veneer with water ripple texture involves a highly controlled and technology-driven process. From raw bamboo selection and carbonization to embossing and surface finishing, every step is critical in delivering a high-quality product suitable for modern architectural needs.
As a factory or B2B supplier, offering stable quality, flexible customization, and reliable export packaging are key to meeting global client demands in the decorative materials industry.
For wholesalers, contractors, and architects looking for eco-friendly, stylish, and functional wall panel solutions, bamboo charcoal water ripple veneer is undoubtedly a material worth investing in.